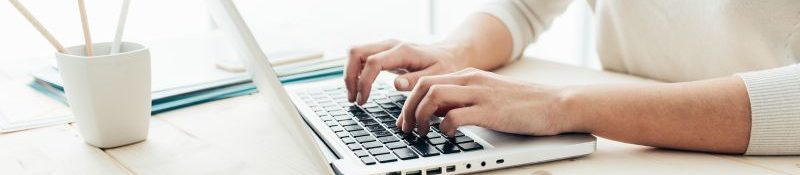
Use Work in Progress (WIP) Finalization in Sage X3: Sage X3 offers the Work in Progress Finalization as a valuable tool for tracking the financial status of unfinished products. WIP represents the accumulated costs of materials, labor, and overhead invested in products still under production. WIP interacts closely with the Inventory, Finance, and Costing modules. It is important to understand these interconnections for effective WIP management.
Key Components of WIP:
1. Accurate Costing: WIP valuation helps determine the precise cost of partially completed goods.
2. Inventory Management: By tracking WIP, you can better manage inventory levels and production planning.
3. Financial Reporting: WIP figures contribute to accurate financial statements.
Important Considerations:
1. Configuration: Sage X3’s WIP functionality can be tailored to specific business needs. To use this functionality effectively with your business requirements, consult your system administrator for details and guidance.
2. Documentation: Refer to Sage X3’s user guides and documentation for in-depth information and procedures.
When a work order is closed but not costed, you may experience errors. You need to run the WIP finalization to get the costing done for the work order
Here are general steps to determine the value of Work-In-Progress
1. Access WIP Module: Navigate to the “WIP” function within the Costing module.
2. Initiate Valuation: Select the “WIP Valuation” option.
3. Define Valuation Criteria: Specify the company, site, and valuation type (e.g., by work order, by product).
4. Set Work Order Range: Indicate the relevant work order range for the calculation.
5. Calculate WIP: Trigger the WIP valuation process.
6. Review Results: Analyze the calculated WIP value.
7. Take Action: Use the results to inform production, inventory, and financial decisions.
8. Document and Report: Maintain records and generate reports as needed.
9. Success Log: A successful valuation will generate a log file detailing processed work orders.