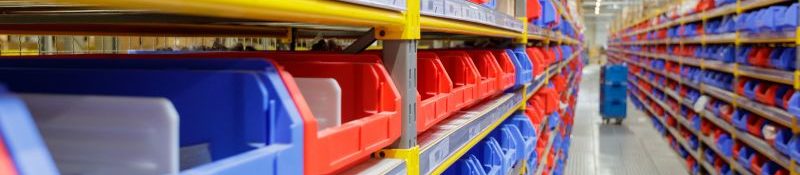
How to Automate Stock Shortage Adjustments for Sales Orders in Sage X3: Efficient inventory management is crucial for smooth order fulfillment. Integrating inventory management with sales order processing in Sage X3 allows the automation of adjustment of shortages in outstanding sales orders. This automation eliminates manual errors, reduces time-consuming tasks, and improves supply chain management. This automation can reduce manual intervention, thereby saving time and resources. It also minimizes errors associated with manual data entry and allocation, ensures timely order fulfilment, and enhances customer satisfaction.
Prerequisites Configuration
1. GENSHT: In the “STO” chapter and “MIS” group, set the “GENSHT” parameter to “Yes”; to enable automatic shortage generation.
2. INIALLORD: In the “VEN” chapter and “SAL” group, set the “INIALLORD” parameter to “Yes”; to initiate automatic allocation of stock to orders.
3. Verify Stock Parameters: Ensure the “Auto process shortages” option is enabled under the “Backorders” tab of the “GESSTE” stock parameters.
4. Customer Setup: Ensure that the customer setup allows partial deliveries to automatically generate shortages when there’s insufficient stock.
Setup and Workflow
1. Navigate to Setup: Go to Setup > Stock > Stock Parameters.
2. Enable Auto-Processing: Check the “Auto process shortages” option under the “Backorders” tab.
3. Create a Sales Order: Input the sales order details.
4. Record Stock Receipt: Create a stock receipt when new stock arrives.
5. Verify Automatic Allocation: The system should now automatically allocate the received stock to fulfill the shortage of the outstanding sales order.
Automating the adjustment of shortages in outstanding sales orders can help streamline inventory management processes in Sage X3.